Fabricating with plastics - what are my options?
- Trem-din
- Sep 23, 2022
- 6 min read
Updated: Dec 21, 2022
Since Alexander Parkes unveiled the first man-made plastic at the Great International Exhibition in London in 1862, the technologies for manufacturing and transforming plastic materials have evolved a lot. In this blog, we are going to review some of the most important ones and learn everything we must take into account when it comes to materializing our ideas. Sometimes, choosing the right manufacturing method can be a crucial decision to make a project viable.
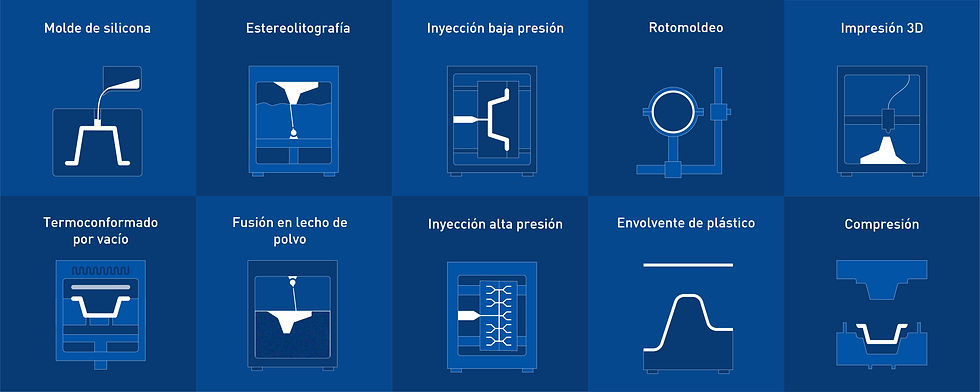
Since the middle of the 20th century, it is impossible to understand industry without the use of plastics: from a water bottle to a piece of furniture or from a microprocessor housing to augmented reality glasses. Plastics make it possible to manufacture products with costs and production cycles that were unthinkable before their appearance.
However, do you know what is best for your project? Today we will help you to decipher it, understand each manufacturing method, and what it is used for, and we will also delve into the decisions that will lead us to know which choice will be the best, such as the number of units (u) to be produced or the cost (€) per unit according to the process.
We will make a description of the existing manufacturing methods for plastics to help us understand their characteristics.
Injection molding
This process consists of introducing a molten polymer under pressure into a mold. When the material fills the cavity, it cools and the mold plates separate, ejecting the already-formed object. Low-pressure and high-pressure injection molding are available.
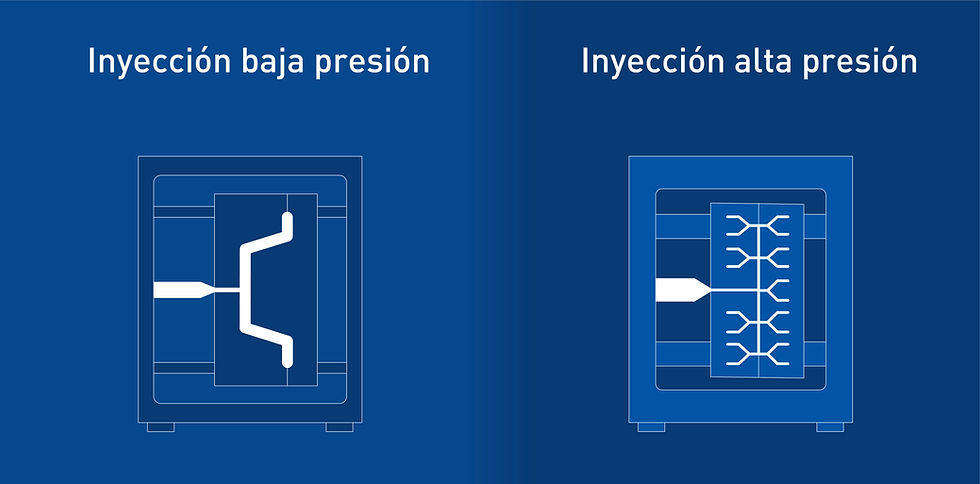
The pressure difference influences many variables:
Material: in low pressure, the materials that can be used are more limited.
Formal design: the shapes that can be generated in low pressure should be simpler. However, high-pressure molding allows more complex shapes to be obtained since it is easier to fill a mold with recesses, thin walls, and narrow channels. Several objects can be obtained from the same mold.
Time: in high-pressure manufacturing, machining the mold requires more time due to its complexity, but production cycles are shorter, so production is faster.
Price: high pressure molds are more expensive, so the initial investment is higher.
3D Printing
3D printing is a set of manufacturing technologies that have developed significantly in recent years. There are different types:
FDM material extrusion
Stereolithography SLA
Powder bed fusion SLS
Digital Light Processing DLP
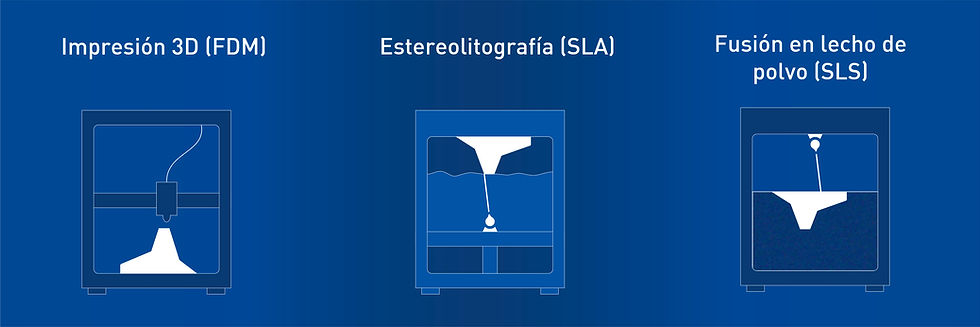
In general, the production time and cost of these methods are usually high, but they do not involve a large initial investment, since they do not require a mold. Therefore, they are very common when generating prototypes and testing them to the correct dimensions. Even so, they are starting to be used more and more for mass production.
The major advantage is that they can generate all kinds of shapes, with recesses, holes, recesses, and complex ribs. This offers the possibility of designing stylized, organic, and attractively shaped products that attract the attention of the buyer and stand out in the market, with the possibility of renewing and improving the designs every few years, with minimal differences in production costs. The main drawback is the finish. In fused deposition printing (FDM), the most common, the surface is marked by layers of material that generate streaks. In stereolithography, on the other hand, the finish is smoother, although the layers may be slightly visible. In the case of powder bed fusion (SLS), the finish is somewhat gritty. However, there are numerous ways to improve the surface finish of the parts, by acid treatment, painting, or polishing, although it should be noted that production time and costs are increased.
These methods are viable for small or not-too-high production volumes, small parts, or very complex or organic shapes. In addition, in methods such as FDM, the range of materials is growing a lot, being able to use additives, metals, or fibers to achieve good mechanical properties, such as the strength of the parts, as well as environmentally friendly plastics that allow in many sectors, such as packaging, a great positioning in the market.
Compression molding
Compression molding is a manufacturing method involving a press that heats and compresses the material into the desired shape. Its use is limited due to cost and shape limitation, as injection molding is generally presented as a more suitable option.

Plastic enveloping
The generation of parts by plastic wrapping is a not very widespread method, although it is an option that is quite feasible in some cases. It consists of folding and machining a plastic sheet. By combining two or more parts that can be assembled, it is possible to obtain boxes and casings.
The main limitations are in the formal design, since the sheets can only be folded in one direction. The range of finishes and materials is also narrower than alternative methods.
It is presented as an alternative to injection molding, since the initial investment is considerably lower, although the price per part is somewhat higher. Therefore, when manufacturing short runs and relatively large objects, it is a viable option.

Vacuum thermoforming
Vacuum thermoforming is used to generate shapes of approximately constant thickness from plastic sheets. The initial investment price for the mold is higher than the envelope or 3D printing, but lower than an injection mold.
The main limitations also lie in the formal design: the sheets from which they are made have a maximum thickness, and therefore limited mechanical properties. Even so, in some cases, subsequent machining can be applied. It is therefore an alternative to injection molding or compression molding, reserved to be applied when the shape allows it.

Silicone mold
In this case, molds made of rubbery materials are used, which can be used up to 25 times, although the best results are guaranteed between 15 and 20 times. The investment to obtain the mold is much lower than other formats, making it a viable option for short runs.
There are limitations in the design, as well as with the type of polymers that can be used. It can work to obtain a prototype or a pre-series, which can later be improved and manufactured, for example, by injection molding in steel molds, where many more units will be needed for profitable production.

Rotomolding
Rotational molding is used to produce empty shapes of approximately constant thickness that are defined by their surface. The polymer is poured into the mold and the mold rotates in all directions to distribute the material.
As with injection molding, a minimum number of units is required for this method to be profitable. Thereafter, the marginal price per unit is quite low. There are quite a few limitations in the shape design, so the product must be adapted for this particular method. Despite this, it has the advantage of allowing very bulky and strong designs, as well as allowing different types of polymers and additives.

How many units (u) will I produce?

To know the approximate number of manufacturing units
The first thing is to know, approximately, the scalability of the project and how many units are to be manufactured. There are customers who require a first stabilization phase and to know the feasibility through testing, which is accessible through plastic fabrication thanks to the large number of options available.
Profitability
The more units produced, the cheaper the unit and the better the return on the initial investment.
Manufacturing method
The manufacturing method will be chosen taking into account the production volume forecast.
Cost per unit by process

As can be seen in the cost comparison chart for the manufacture of plastics by different processes, in terms of units, there are methods adapted to the number of units to be manufactured. For example, it can be seen that high-pressure injection molding is more cost-effective for very long production runs, as is vacuum thermoforming.
Other factors also play a role, which we will explain below.
| Restricciones en el diseño | Acabados superficiales | Materiales |
Inyección | Existen limitaciones geométricas como recovecos, paredes finas y espacios cerrados. Además, el diseño deberá tener ángulos de desmoldeo para poder extraer la pieza del molde. | El acabado se define mecanizando el molde. Conlleva un encarecimiento, pero es posible obtener diferentes variantes, y aplicarlas a una misma pieza. | Pocas restricciones: gran parte de los plásticos son aplicables en este método. |
Impresión 3D (FDM, SLS, SLA...) | La principal restricción del diseño es el tamaño. Es posible generar prácticamente cualquier forma, aunque resulte muy compleja. | El acabado no es controlable, puede ser estriado (FDM), liso (SLA) o arenoso (SLS). Se pueden aplicar pintados, pulidos o alisados con acetona, si el material lo permite. | Al ser una tecnología relativamente reciente, los materiales son limitados, aunque innovadores. Se pueden integrar partículas metálicas para obtener mayor resistencia. |
Rotomoldeo | Permite generar espacios cerrados, pero el grosor de la pieza debe ser constante. | Se define por el molde. El acabado de las superficies internas no es controlable, ya que no está en contacto con el molde. | Pocas restricciones: gran parte de los plásticos son aplicables en este método. |
Envolvente de plástico | Son piezas que parten desde láminas, que sólo pueden curvarse en una única dirección y en un único sentido | Los acabados son limitados, y se aplican con la pintura tras la conformación. Se permiten distintos tipos de granulados. | Pocas restricciones: gran parte de los plásticos son aplicables en este método. |
As we have noted, the plastics manufacturing industry is very broad and allows for a variety of methods, adapted to the shape, product requirements, production volume, etc. There are other factors that are important to control, such as suppliers, alternatives to the use of non-recycled plastics and methods of investment or financing.
Suppliers
Knowing them allows us to find the most efficient solution with the best results for our project. Likewise, there are more factors that influence our decision making. For example, if we want to manufacture a product with different parts, each part may have an ideal manufacturing method, but we would have to deal with several suppliers. Therefore, designing parts adapted to the manufacturing methods can reduce the number of suppliers.
Therefore, designing parts adapted to the manufacturing methods can reduce the number of suppliers, and therefore have greater bargaining power when it comes to obtaining competitive manufacturing prices in the market.
Recycled plastics
Sometimes, parts are sought that do not require very demanding mechanical and aesthetic properties. In these cases, recycled plastics can be used, with the aim of having a more environmentally friendly production. There are also alternatives to high performance polymers that have their origin in biodegradable materials such as PLA (polylactic acid), from renewable and natural raw materials, widely used in 3D printing. Knowing the technical requirements of our project will lead us to choose the most suitable manufacturing method.
Investment and financing
Other factors are due to the investment and future views of the project. Knowing the market, the possibilities of success and the risks, allows us to make the right decision when it comes to manufacturing our product. A short run requires less investment, but if the product works and you want to increase the production volume, it will take more time and money. Sometimes, it is a good idea to generate a prototype or an attractive photorealistic image to look for funding and thus be able to make the decision to start a larger investment with another manufacturing method that brings a higher profitability in the future. Therefore, an analysis of the product and the market will always be necessary to ensure the viability of the project.
These are some of the factors to take into account. From Trem ye accompany and guide you in all parts of this process to achieve optimal results. If you have any questions, you can contact us, without any commitment, we are happy to listen to you.
Comments